Was ist CNC-Bearbeitung?
CNC-Bearbeitung bezeichnet ein Herstellung verfahren zur Bearbeitung von Teilen auf CNC-Werkzeugmaschinen. Die Prozess vorschriften der CNC-Werkzeugmaschinen bearbeitung und der klassischen Werkzeugmaschinen bearbeitung sind im Allgemeinen konsistent, es haben sich jedoch auch wesentliche Änderungen ergeben. Ein mechanisches subtraktives Bearbeitungsverfahren, das digitale Informationen verwendet, um die Verschiebung von Teilen und Werkzeugen zu steuern. Es ist ein effektiver Weg, um die Probleme von variablen Teilen, kleinen Losen, komplexen Formen und hoher Präzision zu lösen und eine hocheffiziente und automatisierte Verarbeitung zu erreichen.
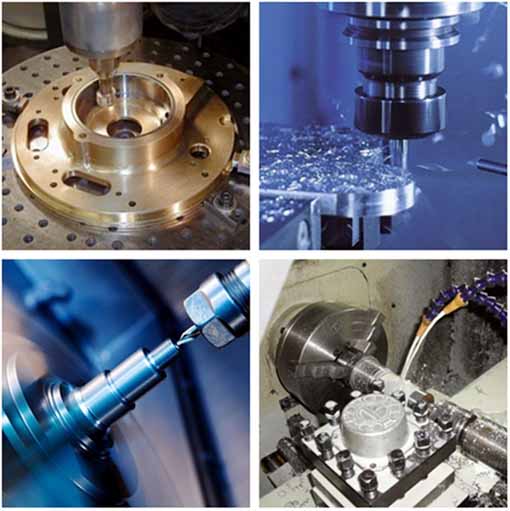
Eine CNC-Werkzeugmaschine ist eine von einem Computer gesteuerte Werkzeugmaschine Der Computer, der zur Steuerung der Werkzeugmaschine verwendet wird, sei es ein Spezialcomputer oder ein Allzweckcomputer, wird zusammenfassend als CNC-System bezeichnet. Die Bewegungen und Hilfsaktionen der CNC-Werkzeugmaschine werden durch die Anweisungen des CNC-Systems gesteuert. Die Anweisungen der numerischen Steuerung werden vom Programmierer entsprechend dem Material des Werkstücks, den Bearbeitungsanforderungen, den Eigenschaften der Werkzeugmaschine und dem vom System vorgegebenen Anweisung format (numerische Steuersprache oder Symbole) zusammengestellt. Das numerische Steuersystem sendet Betriebs- oder Beendigung informationen an die Servovorrichtung und andere Funktion komponenten gemäß den Programm anweisungen, um verschiedene Bewegungen der Werkzeugmaschine zu steuern. Wenn das Teilebearbeitung programm endet, stoppt die Werkzeugmaschine automatisch. Bei jeder Art von CNC-Werkzeugmaschine kann die CNC-Werkzeugmaschine nicht arbeiten, wenn in ihrem CNC-System keine Programmbefehlseingabe vorhanden ist. Zu den gesteuerten Aktionen der Werkzeugmaschine gehören grob das Starten und Stoppen der Werkzeugmaschine; Spindelstart und -stopp, Drehrichtungs- und Drehzahländerung; Richtung, Geschwindigkeit und Modus der Vorschub bewegung; Werkzeugauswahl, Längen- und Radiuskorrektur; Werkzeugwechsel, Kühlmittel öffnen und schließen, etc.
Die kontinuierliche Bahnsteuerung wird auch als Kontursteuerung bezeichnet, die erfordert, dass sich das Werkzeug auf einer vorgegebenen Bahn relativ zum Teil bewegt. Später werden wir energisch punktgesteuerte CNC-Werkzeugmaschinen entwickeln. Punktsteuerung bedeutet, dass sich das Werkzeug von einem Punkt zum anderen bewegt, solange es das Ziel am Ende genau erreichen kann, unabhängig von der Bewegungsroute.
Für die NC-Bearbeitung programmierung gibt es manuelle (manuelle) Programmierung und automatische Programmierung methoden. Manuelle Programmierung, der gesamte Inhalt des Programms wird gemäß dem vom CNC-System vorgegebenen Anweisung format manuell geschrieben. Automatische Programmierung ist Computer programmierung, die in automatische Programmier methoden basierend auf Sprache und Zeichnung unterteilt werden kann. Unabhängig von der Art des automatischen Programmieren verfahrens ist jedoch entsprechende Hard- und Software erforderlich.
Es zeigt sich, dass die Umsetzung der CNC-Bearbeitung programmierung der Schlüssel ist. Aber Programmieren allein reicht nicht aus: Zur CNC-Bearbeitung gehören auch eine Reihe von Vorarbeiten, die vor der Programmierung und nach der Programmierung zu erledigen sind. Im Allgemeinen sind die Hauptinhalte des CNC-Bearbeitung prozesses wie folgt:
⑴ Wählen und bestätigen Sie die Teile und Inhalte für die CNC-Bearbeitung;
⑵ Prozessanalyse der CNC-Bearbeitung von Teile zeichnungen;
⑶ Prozessgestaltung der CNC-Bearbeitung;
⑷ Mathematische Bearbeitung von Teilezeichnungen;
⑸ Erstellen Sie die Liste der Verarbeitungsverfahren;
⑹ Stellen Sie das Kontroll medium gemäß der Verfahrensliste her;
⑺ Überprüfen und ändern Sie das Programm;
⑻ Probe bearbeitung von Prototypen und Problem behandlung vor Ort;
⑼ Erstellung und Ablage von CNC-Bearbeitung prozess dokumenten.
Um den Automatisierungsgrad der Produktion zu verbessern, die Programmierzeit zu verkürzen und die Kosten der CNC-Bearbeitung zu senken, wurden eine Reihe fortschrittlicher CNC-Bearbeitung technologien entwickelt und in der Luft- und Raumfahrtindustrie eingesetzt. B. eine numerische Computersteuerung, das heißt, ein Klein- oder Mikrocomputer wird verwendet, um die Steuerung in dem numerischen Steuerung system zu ersetzen, und die im Computer gespeicherte Software wird verwendet, um Berechnungs- und Steuerfunktionen auszuführen. Diese Art von Soft-Connected-Computer-Numerical-Control-System ersetzt nach und nach das Numerical-Control-System im Anfangszustand. Direkte numerische Steuerung bedeutet, einen Computer zu verwenden, um mehrere numerisch gesteuerte Werkzeugmaschinen direkt zu steuern, was für die Kleinserien- und Kurztakt produktion von Flugzeugen sehr geeignet ist. Das ideale Steuersystem ist ein adaptives Steuersystem, das Verarbeitungsparameter kontinuierlich ändern kann.Obwohl das System selbst komplex und teuer ist, kann es die Verarbeitung effizienz und -qualität verbessern. Neben der hardwaremäßigen Verbesserung von CNC-Systemen und Werkzeugmaschinen hat die CNC-Entwicklung einen weiteren wichtigen Aspekt, nämlich die Entwicklung von Software. Computergestützte Programmierung (auch automatische Programmierung genannt) bedeutet, dass, nachdem ein Programmierer ein Programm in numerischer Steuerung sprache geschrieben hat, dieses zur Übersetzung in den Computer eingegeben wird und der Computer es schließlich automatisch ausgibt. Die am weitesten verbreitete CNC-Sprache ist die APT-Sprache. Es gliedert sich grob in ein Haupt bearbeitung programm und ein Nach bearbeitung programm. Ersteres übersetzt das vom Programmierer geschriebene Programm und berechnet die Werkzeugbahn;Letzterer übersetzt die Werkzeugbahn in ein Teile bearbeitung programm einer CNC-Werkzeugmaschine.
Numerische Steuerung verarbeitung besteht darin, ein Programm auf den Computer zu schreiben, bevor das Werkstück verarbeitet wird. Geben Sie diese Programme dann in die Werkzeugmaschine ein, die von dem Computerprogramm zur Befehlsverarbeitung gesteuert wird. Oder schreiben Sie direkt Anweisungen für die CNC-Bearbeitung auf dem von diesem Computerprogramm gesteuerten Bedienfeld der Werkzeugmaschine. Der Bearbeitungsprozess umfasst: Werkzeug vorschub, Werkzeugwechsel, Geschwindigkeit wechsel, Richtung wechsel, Stopp usw., die alle automatisch abgeschlossen werden. Die CNC-Bearbeitung ist eine fortschrittliche Methode der modernen Formenherstellung und -bearbeitung. Natürlich müssen CNC-Bearbeitungsverfahren nicht nur für die Formteilbearbeitung eingesetzt werden, sondern haben auch ein breites Einsatzspektrum.
1. Die Dimensionierung sollte den Eigenschaften der CNC-Bearbeitung entsprechen
Bei der CNC-Programmierung basieren die Größe und Position aller Punkte, Linien und Flächen auf dem Programmier ursprung. Daher ist es am besten, die Koordinaten größe direkt in der Teilezeichnung anzugeben oder zu versuchen, die Größe mit demselben Bezugspunkt anzugeben.
2. Die Bedingungen der geometrischen Elemente sollten vollständig und genau sein
Bei der Programmierung muss der Programmierer die Parameter der geometrischen Elemente, die die Kontur des Teils und die Beziehung zwischen den geometrischen Elementen bilden, vollständig erfassen. Da bei der automatischen Programmierung alle geometrischen Elemente der Kontur des Teils definiert werden müssen, müssen bei der manuellen Programmierung die Koordinaten jedes Knotens berechnet werden. Egal welcher Punkt unklar oder ungewiss ist, eine Programmierung kann nicht durchgeführt werden. Aufgrund unzureichender Berücksichtigung oder Vernachlässigung durch Teile konstrukteure im Konstruktionsprozess gibt es jedoch oft unvollständige oder unklare Parameter wie Bogen und Gerade, Bogen und Bogen, unabhängig davon, ob sie tangential sind oder sich schneiden oder getrennt sind. Daher müssen Sie bei der Überprüfung und Analyse der Zeichnungen vorsichtig sein und sich rechtzeitig an den Konstrukteur wenden, wenn Sie Probleme feststellen.
3. Zuverlässige Positionierung referenz
In der CNC-Bearbeitung sind die Bearbeitungsprozesse oft konzentriert und es ist sehr wichtig, sie auf derselben Basis zu verorten. Daher ist es oft erforderlich, einige Hilfsbezugspunkte festzulegen oder einige Prozessvorsprünge auf dem Rohling hinzuzufügen.
4. Einheitlicher Geometrietyp oder -größe
Es ist am besten, einen einheitlichen geometrischen Typ oder eine einheitliche Größe für die Form und die innere Kavität des Teils zu verwenden, damit die Anzahl der Werkzeugwechsel reduziert und das Programm gesteuert werden kann, um die Länge des Programms zu verkürzen.
Die Form der Teile ist so symmetrisch wie möglich, was für die Programmierung mit der Spiegel bearbeitung funktion der CNC-Werkzeugmaschine praktisch ist, um Programmierzeit zu sparen.
1. Die Grundprinzipien der Positionierung und Installation
Bei der Bearbeitung von Teilen auf einer CNC-Werkzeugmaschine besteht das Grundprinzip der Positionierung und Montage darin, einen sinnvollen Positionsbezug und Aufspannplan zu wählen. Achten Sie bei der Auswahl auf folgende Punkte:
1. Streben Sie nach einem einheitlichen Benchmark für Konstruktions-, Prozess- und Programmier berechnungen.
2. Minimieren Sie die Anzahl der Spannzeiten und bearbeiten Sie nach dem Positionieren und Spannen möglichst alle zu bearbeitenden Flächen einmal.
3. Vermeiden Sie die Verwendung von CNC-Bearbeitung schemata, die nach dem Herunterfahren manuell angepasst werden. Sollte die Effektivität von CNC-Werkzeugmaschinen voll ausspielen.
zwei, Grundprinzipien für die Auswahl von Vorrichtungen
Die Eigenschaften der CNC-Bearbeitung stellen zwei grundlegende Anforderungen an die Vorrichtung:
Eine besteht darin, sicherzustellen, dass die Koordinatenrichtung der Spannvorrichtung relativ zur Koordinatenrichtung der Werkzeugmaschine festgelegt ist;
Die zweite besteht darin, die Größenbeziehung zwischen den Teilen und dem Maschinen koordinatensystem zu koordinieren. Darüber hinaus sollten folgende Punkte beachtet werden:
1. Wenn die Teilecharge nicht groß ist, sollten so oft wie möglich modulare Vorrichtungen, verstellbare Vorrichtungen und andere allgemeine Vorrichtungen verwendet werden. Um die Produktionsvorbereitung zeit zu verkürzen und Produktionskosten zu sparen.
2. Berücksichtigen Sie bei der Massenproduktion nur die Verwendung spezieller Vorrichtungen und bemühen Sie sich um eine einfache Struktur.
3. Das Be- und Entladen von Teilen sollte schnell, bequem und zuverlässig sein, um die Maschinenstoppzeit zu verkürzen.
4. Die Teile auf der Vorrichtung dürfen die Bearbeitung der Oberflächen der Teile durch die Werkzeugmaschine nicht behindern, dh die Vorrichtung sollte geöffnet sein. Seine Positionierungs- und Klemm mechanismus komponenten können das Schneiden während der Bearbeitung (wie Kollision usw.) nicht beeinträchtigen.
CNC-Bearbeitungsfehler △ Nummer:
Es besteht aus Programmierfehler △ Bearbeitung, Werkzeug maschinen fehler △ Maschine, Positionier fehler △ behoben, Werkzeug einstellung fehler △ und anderen Fehlern.
Nämlich: △Zahl plus = f (△ Bearbeiten + △ Maschine + △ Fest + △ Messer)
in:
1. Programmierfehler △ setzt sich zusammen aus Näherungsfehler δ und Rundungsfehler. Der Approximations fehler δ entsteht bei der Approximation einer nicht kreisförmigen Kurve mit einem geraden Streckenabschnitt oder einem Kreisbogenabschnitt, wie in Abbildung 1.43 dargestellt. Der Rundungsfehler ist der Fehler, der durch Runden des Koordinaten werts auf einen ganzzahligen impuls äquivalenten Wert während der Daten verarbeitung erzeugt wird. Impuls äquivalent bezieht sich auf die Verschiebung jedes Einheitsimpulses entsprechend der Koordinatenachse. Normale Präzisions-CNC-Werkzeugmaschinen, der allgemeine Impuls äquivalen twert beträgt 0,01 mm; Der Puls äquivalent wert von präziseren CNC-Werkzeugmaschinen beträgt 0,005 mm oder 0,001 mm usw.
2. Der Fehler der Werkzeugmaschine wird durch den Fehler des CNC-Systems und des Vorschub systems verursacht.
3. Der Positionier fehler △ wird immer dann verursacht, wenn das Werkstück auf der Vorrichtung positioniert ist und die Vorrichtung auf der Werkzeugmaschine positioniert ist.
4. Werkzeug einstellung fehler △ Werkzeug wird bei der Bestimmung der relativen Position von Werkzeug und Werkstück erzeugt.
Programmstruktur
Ein Programmsegment ist eine fortlaufende Wortgruppe, die als Einheit verarbeitet werden kann, und es ist eigentlich ein Abschnitt eines Programms in einem CNC-Bearbeitung programm. Der Hauptteil des Teile bearbeitung programms besteht aus mehreren Programm abschnitten. Die meisten Programm segmente werden verwendet, um die Werkzeugmaschine anzuweisen, eine bestimmte Aktion abzuschließen oder auszuführen. Der Programmteil ist: Es besteht aus Größen wörtern, Nicht größen wörtern und Blockende befehlen. Beim Schreiben und Drucken belegt jeder Block im Allgemeinen eine Zeile und das gleiche gilt, wenn das Programm auf dem Bildschirm angezeigt wird.
Programm-Format
Ein konventionelles CNC-Bearbeitung programm besteht aus Startsymbol (einzelne Zeile), Programmname (einzelne Zeile), Programm rumpf und Programmende anweisung (im Allgemeinen einzeilig). Am Ende des Programms steht ein Programmende zeichen. Das Programmstartzeichen und das Programmende zeichen sind die gleichen Zeichen: % im ISO-Code, ER im EIA-Code. Der Programmende befehl kann M02 (Programmende) oder M30 (Papier bandende) sein. CNC-Werkzeugmaschinen verwenden im Allgemeinen gespeicherte Programme zum Ausführen.Zu diesem Zeitpunkt sind die gemeinsamen Punkte von M02 und M30: Nach Beendigung aller anderen Befehle im Satz werden Spindel, Kühlmittel und Vorschub gestoppt und die Steuerung zurückgesetzt. M02 und M30 sind bei einigen Werkzeugmaschinen (Systemen) völlig gleichwertig, während die folgenden Unterschiede bei anderen Werkzeugmaschinen (Systemen) verwendet werden: Wenn das Programm mit M02 beendet wird, stoppt der Cursor am Ende des Programms, nachdem der Automatikbetrieb beendet ist; Bei Verwendung von M3O zum Beenden des Programm betriebs können die Cursor- und Bildschirmanzeige nach Beendigung des Automatikbetriebs automatisch zum Anfang des Programms zurückkehren und das Programm kann durch Drücken der Starttaste erneut ausgeführt werden. Obwohl M02 und M30 einen Block mit anderen Programm wörtern teilen dürfen, ist es besser, sie in einem einzigen Block aufzulisten oder einen Block nur mit der Sequenznummer zu teilen.
Der Programmname steht vor dem Hauptteil des Programms und nach dem Programmstart und nimmt normalerweise eine eigene Zeile ein. Der Programmname hat zwei Formen: Einer besteht aus vorgeschriebenen englischen Zeichen (normalerweise O), gefolgt von mehreren Ziffern. Die maximal zulässige Anzahl von Stellen ist im Handbuch festgelegt, und die beiden gebräuchlichen sind zweistellig und vierstellig. Diese Form des Programmnamens kann auch als Programmnummer bezeichnet werden. Eine andere Form besteht darin, dass der Programmname aus englischen Zeichen, Zahlen oder einer Mischung aus Englisch und Zahlen besteht und in der Mitte ein „-“-Zeichen hinzugefügt werden kann. Dieses Formular macht das Verfahren der Benutzer Umbenennen flexibler. Das Programm für den dritten Bearbeitung vorgang des Flansches mit der Teilezeichnung nummer 215 auf der CNC-Drehmaschine LC30 kann beispielsweise LC30-FIANGE-215-3 heißen. Dies bringt großen Komfort bei Verwendung, Lagerung und Abruf. Die Form des Programmnamens wird vom CNC-System bestimmt.
%
O1001
N0 G92 X0 Y0 Z0
N5 G91 G00 X50 Y35 S500 MO3
N10 G43 Z-25 T01.01
N15 G01 G007 Z-12
N20 G00 Z12
N25 X40
N30 G01 Z-17
N35 G00 G44 Z42 M05
N40 G90 X0 Y0
N45 M30
%
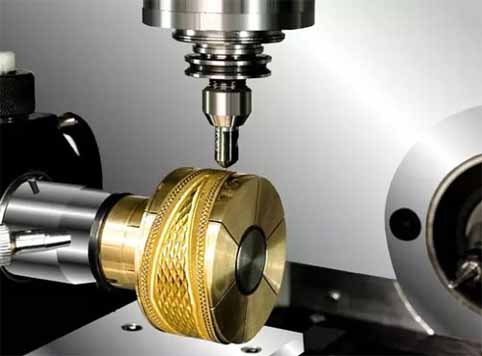
Segment-Format
Die Regeln für die Anordnung von Wörtern, Zeichen und Daten in einem Programm abschnitt werden als Block format bezeichnet. Das feste Sequenz format und das Trennzeichen format (HT oder TAB) wurden in der Geschichte der CNC verwendet. Wenn diese beiden Programm segment formate bestanden sind, wird das variable Programm segment format der Wortadresse im In- und Ausland weit verbreitet verwendet, auch als Wort adressen format bekannt. Bei diesem Format ist die Programm wortlänge nicht fest und auch die Anzahl der Programmworte ist variabel.Die meisten CNC-Systeme erlauben eine beliebige Anordnung der Programm wortreihenfolge, sie gehört also zum variablen Satz format. In den meisten Fällen werden jedoch zur Vereinfachung des Schreibens, Eingebens, Prüfens und Korrekturlesens Programm wörter verwendet, um im Programm segment in einer bestimmten Reihenfolge anzuordnen. Das Programmierhandbuch der CNC-Werkzeugmaschine verwendet ein detailliertes Format, um die Details der Programm ierung zu klassifizieren und festzulegen: Die bei der Programm ierung verwendeten Zeichen, die Reihenfolge und Wortlänge der Programm wörter im Programm segment usw. Z.B:
/ NO3 G02 X+053 Y+053 I0 J+053 F031 S04 T04 M03 LF
Die detaillierte Format klassifizierung des obigen Beispiels sieht wie folgt aus: N03 ist die Sequenznummer des Programm segments; G02 bedeutet, dass die Bearbeitung spur ein Bogen im Uhrzeigersinn ist; X+053, Y+053 geben die Koordinaten des Endpunkts des zu bearbeitenden Bogens an; I0, J+053 stellen die Mittelpunkt koordinaten des zu verarbeitenden Bogens dar; F031 ist die Vorschubgesch windigkeit der CNC-Bearbeitung; S04 ist die Spindeldrehzahl; T04 ist die Werkzeugnummer des verwendeten Werkzeugs; M03 ist ein Hilfsfunktion befehl; LF-Blockende-Befehl; / ist ein Sprungau wahl befehl. Die Funktion des Auswahl befehls überspringen ist: Unter der Prämisse, dass das Programm unverändert bleibt, kann der Bediener wählen, ob er die Blöcke im Programm mit Anweisungen zum Überspringen der Auswahl ausführen möchte oder nicht. Die Auswahlmethode besteht in der Regel darin, den Auswahlschalter zum Überspringen auf dem Maschinen bedienfeld auf ON oder OFF zu stellen, um die Nichtausführung oder die Ausführung des Satzes mit "/" zu realisieren.
Programm ausführen
Diese Situation tritt manchmal beim Kompilieren eines CNC-Bearbeitung programms auf: Eine Gruppe von Programm segmenten kommt in einem Programm mehrfach vor oder muss in mehreren Programmen verwendet werden. Wir können diese Gruppe von Programm segmenten extrahieren, benennen und separat speichern, diese Gruppe von Programm segmenten sind Unterprogramme. Ein Unterprogramm ist ein Abschnitt eines Verarbeitung programms, das durch entsprechende Maschinen steuerung befehle aufgerufen werden kann, und hat im Allgemeinen eine unabhängige Bedeutung bei der Verarbeitung. Das Verarbeitung programm, in dem sich die Anweisung zum Aufrufen des Unterprogramms der ersten Ebene befindet, wird als Hauptprogramm bezeichnet. Der Befehl zum Anpassen des Unterprogramms ist auch ein Programm abschnitt, der im Allgemeinen aus dem Unterprogrammaufruf befehl, dem Namen des Unterprogramms und der Anzahl der Aufrufe besteht. Die spezifischen Regeln und Formate variieren von System zu System, zum Beispiel ist es auch „unterprogramm Nr. 55 einmal aufrufen“, das FANUC-System verwendet „M98 P55.“ und das amerikanische A-B-Firmensystem verwendet „P55x“.
Unterprogramme können verschachtelt werden, dh Schicht für Schicht. Die Beziehung zwischen der oberen Ebene und der nächsten Ebene ist dieselbe wie die Beziehung zwischen dem Hauptprogramm und dem Unterprogramm der ersten Ebene. Die maximal einstellbare Lagenanzahl hängt vom jeweiligen CNC-System ab. Form und Aufbau des Unterprogramms entsprechen in etwa dem Hauptprogramm: Die erste Zeile ist die Unter programmnummer (Name), die letzte Zeile ist die Anweisung "Unter programmende" und dazwischen der Unter programm rumpf. Die Funktion der Hauptprogramm-Ende-Anweisung besteht jedoch darin, das Hauptprogramm zu beenden und das CNC-System zurückzusetzen. Seine Anweisungen wurden standardisiert und alle Systeme verwenden M02 oder M30; Und die Funktion des Unterprogramm-Ende-Befehls besteht darin, das Unterprogramm zu beenden, zum Hauptprogramm oder dem Unterprogramm der höheren Ebene zurückzukehren. Die Befehle sind in verschiedenen Systemen nicht einheitlich, wie M99 für das FANUC-System, M17 für das Siemens-System, M02 für das System der amerikanischen A-B-Firma usw.
Benutzermakros (Programme) können in CNC-Bearbeitung programmen verwendet werden. Das sogenannte Makroprogramm ist ein Unterprogramm, das Variablen enthält. Der Befehl, der das Makroprogramm im Programm aufruft, wird als Benutzer makrobefehl bezeichnet, und die Funktion, die das System mit dem Benutzermakro programm verwenden kann, wird als Benutzermakro funktion bezeichnet. Bei der Ausführung müssen Sie nur den Benutzer makrobefehl schreiben, um seine Benutzermakro funktion auszuführen.
Die größten Funktionen von Benutzermakros sind:
● Variablen können in Benutzermakros verwendet werden;
● Sie können Berechnung formeln, Steuerung anweisungen und verschiedene Funktionen verwenden
● Sie können Benutzer makrobefehle verwenden, um Variablen Werte zuzuweisen.
Die CNC-Werkzeugmaschine verwendet Gruppen technologie zur Bearbeitung von Teilen, wodurch die Losgröße erweitert, der Programmier aufwand reduziert und die Wirtschaftlichkeit verbessert werden kann. Bei der Gruppen bearbeitung werden die Teile klassifiziert und das Bearbeitung programm für diese Art von Teilen kompiliert, anstatt für jedes Teil ein Programm zu editieren. Bei der Verarbeitung der gleichen Art von Teilen mit unterschiedlichen Größen besteht der Hauptvorteil der Verwendung von Benutzermakros darin, dass Variablen anstelle von bestimmten Werten verwendet werden können. Wenn es um die eigentliche Verarbeitung geht, weisen Sie der Variablen einfach den tatsächlichen Größenwert dieses Teils mit dem Benutzer makrobefehl zu.
Prinzipien der CNC-Bearbeitung
⑴ Die Bearbeitung des vorherigen Prozesses hat keinen Einfluss auf das Positionieren und Spannen des nächsten Prozesses.
⑵ Zuerst innen, dann außen, dh zuerst wird die innere Kavität (inneres Loch) und dann die äußere Form bearbeitet.
⑶ Der Bearbeitungsprozess mit der gleichen Anlage oder mit dem gleichen Werkzeug sollte kontinuierlich durchgeführt werden, um Fehler durch Neu positionierung oder Werkzeugwechsel zu reduzieren.
⑷ In der gleichen Anlage sollte zuerst der Vorgang durchgeführt werden, der wenig Einfluss auf die Steifigkeit des Werkstücks hat.

Bearbeitungsweg
Die Bearbeitung strecke Vorschub der CNC-Drehmaschine bezeichnet den Weg, den das Drehwerkzeug vom Werkzeugeinstellpunkt (bzw. dem festen Nullpunkt der Werkzeugmaschine) bis zu diesem Punkt zurückfährt und das Bearbeitung programm beendet. Inklusive Schnittwege und spanlose Leerwege wie Schneiden und Ausschneiden durch das Werkzeug.
Der Vorschub weg beim Schlichten erfolgt grundsätzlich entlang der Teile konturfolge. Daher liegt der Schwerpunkt bei der Bestimmung der Vorschub route auf der Bestimmung der Vorschub route für die Schrupp bearbeitung und den Leerhub.
Bei der CNC-Drehmaschinen bearbeitung folgt die Bestimmung der Bearbeitung route im Allgemeinen den folgenden Prinzipien.
① Sie sollte die Genauigkeit und Oberflächenrauheit des zu bearbeitenden Werkstücks gewährleisten können.
② Machen Sie den Verarbeitung weg so kurz wie möglich, reduzieren Sie die Leerlaufzeit und verbessern Sie die Verarbeitung effizienz.
③ Versuchen Sie, den Arbeitsaufwand bei der numerischen Berechnung zu vereinfachen und den Verarbeitung prozess zu vereinfachen.
④ Für einige wiederverwendbare Programme sollten Unterprogramme verwendet werden.
Machen Sie das Verarbeitung programm über den kürzesten Vorschub weg, können Sie nicht nur die Ausführungszeit des gesamten Verarbeitung prozesses einsparen. Es kann auch unnötigen Werkzeugverbrauch und Verschleiß der gleitenden Teile des Vorschub mechanismus der Werkzeugmaschine reduzieren. Die Typen und Implementierung methoden der kürzesten Feedroute sind wie folgt:
⑴ Der kürzeste Schnitt vorschub weg. Der kürzeste Schnitt vorschub weg kann die Produktionseffizienz effektiv verbessern und den Werkzeugverlust reduzieren. Bei der Gestaltung des kürzesten Schnitt vorschub weges ist auch auf die Steifigkeit des Werkstücks und die bearbeitung technischen Anforderungen zu achten.
⑵ Die kürzeste Leerfahrtroute.
① Den Ausgangspunkt der Bearbeitung geschickt nutzen.
Ein Beispiel für eine allgemeine Situation beim Schruppen im Rechteck schleifenmodus. Die Einstellung der Werkzeugspitze A soll der Notwendigkeit eines bequemen Werkzeugwechsels bei der Schlichtbearbeitung und anderen Bearbeitung prozessen Rechnung tragen, so dass sie weit vom Rohling entfernt liegt. Gleichzeitig den Startpunkt mit dem Werkzeugeinstellpunkt abgleichen
② Stellen Sie den CNC-Werkzeugwechselpunkt geschickt ein.
Um den Komfort und die Sicherheit des Werkzeugwechsels zu berücksichtigen, wird der Werkzeugwechselpunkt manchmal auch weit vom Rohling entfernt gesetzt. Dann wird beim Wechsel des zweiten Messers der Leerweg beim Feindrehen zwangsläufig länger; Wird der Werkzeugwechselpunkt des zweiten Werkzeugs ebenfalls auf die Nicht-Punkt-Position in der Mitte gesetzt, kann die Leerhubstrecke verkürzt werden.
③ Die CNC-Route "Rückkehr auf Null" sinnvoll gestalten. Um den Berechnung prozess zu vereinfachen und die Überprüfung beim manuellen Erstellen des Bearbeitung programms der komplexen Kontur zu erleichtern, führt der Programmierer manchmal nach jeder Bearbeitung die Operation "Rückkehr auf Null" für den Endpunkt des Werkzeugs aus. Lassen Sie alles an die Position des Werkzeu geinstell punktes zurückkehren und führen Sie dann das nachfolgende Programm aus. Dies erhöht den Abstand des Zufuhrpfads und verringert die Produktion effizienz. Daher sollte bei einer rationellen Anordnung der Route "Zurück zu Null" der Abstand zwischen dem Endpunkt des vorherigen Schnitts und dem Startpunkt des nächsten Schnitts so kurz wie möglich sein. Oder Null, um die Anforderung des kürzesten Vorschubwegs zu erfüllen. Verwenden Sie außerdem bei der Auswahl des Befehls zum Zurückkehren zum Werkzeugeinstellpunkt unter der Voraussetzung, dass keine Störung vorliegt, den bidirektionalen Befehl "Rückkehr auf Null" der x- und z-Achse so oft wie möglich gleichzeitig. Der Weg der Funktion "zurück auf Null" ist der kürzeste.
⑶ Schritt CNC-Schneid vorschubweg des Rohlings mit großem Rand. Es werden zwei Schnittvorschub wege für Zuschnitte mit zu viel Rand aufgelistet. Es ist der falsche Schritt-Schneidweg: Schneiden in der Reihenfolge von 1 Eimer und 5, der verbleibende Rand für jeden Schnitt ist gleich, was der richtige Schritt-Schneid vorschubweg ist. Denn unter gleicher Schnittstärke.
⑷ Kontinuierlicher Schnittvorschubweg für die Schlichtteilkontur. Das Schlichten der Kontur des Teils kann mit einem oder mehreren Schlichtvorgängen erfolgen. Die fertige Kontur soll durch den letzten Schnitt kontinuierlich bearbeitet werden. Zu diesem Zeitpunkt sollten die Vorwärts- und Rückwärtspositionen des Werkzeugs geeignet ausgewählt werden. Versuchen Sie, Schnitt und Schnitt bzw. Werkzeugwechsel und Pause nicht in einer kontinuierlichen Kontur anzuordnen, um das Gleichgewicht des Prozesssystems nicht durch plötzliche Schnittkraftänderungen zu beschädigen. Verursachen Sie Kratzer, Formmutationen oder bleibende Werkzeugspuren auf der Kontur des Teils.
⑸ Spezieller Zuführungsweg. In der CNC-Drehbearbeitung unter normalen Umständen. Der Längsvorschub des Werkzeugs erfolgt in negativer Richtung der Koordinate, aber manchmal ist es nicht sinnvoll, den Vorschubweg entsprechend seiner normalen negativen Richtung anzuordnen. Es kann sogar das Werkstück beschädigen.
① Die Anzahl der Werkzeuge wird stark reduziert und komplexe Werkzeuge sind für die Bearbeitung von Teilen mit komplexen Formen nicht erforderlich. Wenn Sie die Form und Größe des Teils ändern möchten, müssen Sie nur das Teilebearbeitungsprogramm ändern, das für die Entwicklung und Modifikation neuer Produkte geeignet ist.
② Die Bearbeitungsqualität ist stabil, die Bearbeitungsgenauigkeit ist hoch und die Wiederholgenauigkeit ist hoch, was für die Bearbeitungsanforderungen von Flugzeugteilen geeignet ist.
③ Bei der Mehrsorten- und Kleinserienfertigung ist die Produktionseffizienz höher, was die Zeit für die Produktionsvorbereitung, die Werkzeugmaschineneinstellung und die Prozessinspektion verkürzen kann, und die Schnittzeit wird durch die Verwendung der besten Schnittmenge reduziert .
④ Es kann komplexe Oberflächen bearbeiten, die mit herkömmlichen Methoden schwer zu bearbeiten sind, und sogar einige unbeobachtbare Bearbeitungsteile bearbeiten. Der Nachteil der CNC-Bearbeitung besteht darin, dass die Werkzeugmaschinen teuer sind und ein hohes Maß an Wartungspersonal erfordern.
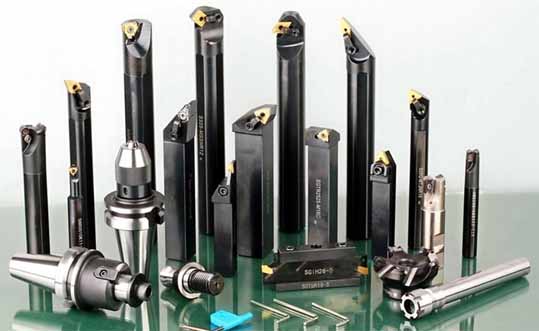
Die Standzeit hängt eng mit dem Zerspanvolumen zusammen. Bei der Formulierung von Schnittparametern sollte zunächst die sinnvolle Standzeit gewählt und die sinnvolle Standzeit entsprechend dem Optimierungsziel ermittelt werden. Im Allgemeinen unterteilt in die Werkzeugstandzeit mit der höchsten Produktivität und die Werkzeugstandzeit mit den niedrigsten Kosten. Ersteres wird nach dem Ziel der geringsten Einzelstück-Mannstunden und letzteres nach dem Ziel der niedrigsten Prozesskosten bestimmt.
Bei der Wahl der Standzeit können Sie je nach Komplexität des Werkzeugs, Fertigungs- und Schleifkosten folgende Punkte berücksichtigen. Die Standzeit von komplexen und hochpräzisen Werkzeugen sollte höher gewählt werden als die von einschneidigen Werkzeugen. Bei Wendeschneid werkzeugen mit Maschinenklemmung kann aufgrund der kurzen Werkzeugwechselzeit, um die Schneidleistung voll auszuschöpfen und die Produktionseffizienz zu verbessern, die Werkzeugstandzeit niedriger gewählt werden, in der Regel 15-30 Minuten. Bei Multitools, modularen Werkzeug maschinen und automatisierten Bearbeitung werkzeugen mit komplexer Werkzeug installation, Werkzeugwechsel und Werkzeug einstellung soll die Standzeit höher sein und insbesondere die Zuverlässigkeit des Werkzeugs gewährleistet sein. Wenn die Produktivität eines bestimmten Prozesses in der Werkstatt die Verbesserung der Produktivität der gesamten Werkstatt begrenzt, sollte die Werkzeugstandzeit des Prozesses niedriger gewählt werden. Bei großen Kosten der Gesamtanlage, die sich auf eine bestimmte Prozesseinheit Zeit teilen, sollte auch die Werkzeugstandzeit geringer gewählt werden. Um beim Schlichten großer Teile sicherzustellen, dass mindestens ein Durchgang abgeschlossen ist und das Werkzeug nicht mitten im Schnitt gewechselt wird, sollte die Standzeit entsprechend der Genauigkeit des Teils und der Oberflächenrauheit bestimmt werden. Im Vergleich zu herkömmlichen Werkzeug maschinen bearbeitung verfahren stellt die CNC-Bearbeitung höhere Anforderungen an die Zerspanungswerkzeuge. Es muss nicht nur steif und hochpräzise sein, sondern erfordert auch stabile Abmessungen, hohe Lebensdauer und gleichzeitig einfache Montage und Einstellung für die Brech- und Austragsleistung, um den hohen Effizienzanforderungen von CNC-Werkzeugmaschinen gerecht zu werden. Die ausgewählten Werkzeuge auf CNC-Werkzeugmaschinen verwenden häufig hoch geschwindigkeit geeignete Werkzeug materialien (z. B. Schnellarbeitsstahl, Feinstkorn-Hartmetall) und verwenden Wendeschneidplatten.
2. Wählen Sie Werkzeuge zum CNC-Drehen
Die gebräuchlichen CNC-Dreh werkzeuge werden im Allgemeinen in drei Typen unterteilt: Umform Drehen werkzeuge, Spitz Drehen werkzeuge, Bogen drehwerkzeuge und drei Typen. Umformende Drehwerkzeuge werden auch Prototypen drehwerkzeuge genannt, und die Konturform der bearbeiteten Teile wird vollständig durch die Form und Größe der Schneidkante des Drehwerkzeugs bestimmt. In der CNC-Drehbearbeitung umfassen gängige Umform drehwerkzeuge Bogen drehwerkzeuge mit kleinem Radius, nicht rechteckige Drehwerkzeuge und Gewindewerkzeuge. Bei der CNC-Bearbeitung sollte das Umform drehwerkzeug so wenig wie möglich eingesetzt werden oder nicht. Der Spitzdrehmeißel ist ein Drehmeißel, der sich durch eine gerade Schneide auszeichnet. Die Spitze dieses Drehmeißeltyps besteht aus linearen Haupt- und Nebenschneiden: Zum Beispiel 900 Innen- und Außendreh werkzeuge, linke und rechte Stirndrehwerkzeuge, Stech- (Schneid-)Drehwerkzeuge und verschiedene Außen- und Innendrehwerkzeuge mit sehr kleinen Spitzenfasen.
Die Auswahl der geometrischen Parameter des spitzen Drehwerkzeugs (hauptsächlich des geometrischen Winkels) ist im Wesentlichen die gleiche wie beim gewöhnlichen Drehen: Die Eigenschaften der CNC-Bearbeitung (wie Bearbeitung route, Bearbeitung störungen usw.) sollten jedoch vollständig berücksichtigt werden, und die Festigkeit der Werkzeugspitze selbst sollte berücksichtigt werden.
zwei, Bogenförmiges Drehwerkzeug. Der bogenförmige Drehmeißel ist ein Drehmeißel, der sich durch eine bogenförmige Schneide mit einem kleinen Rundheits- oder Linienprofilfehler auszeichnet. Jeder Punkt der Bogenkante des Drehmeißels stellt die Spitze des bogenförmigen Drehmeißels dar. Dementsprechend liegt der Werkzeugpositionspunkt nicht auf dem Bogen, sondern in der Mitte des Bogens. Der bogenförmige Drehmeißel kann zum Drehen von Innen- und Außenflächen verwendet werden und eignet sich besonders zum Drehen verschiedener glatter (konkaver) Umformflächen. Bei der Wahl des Bogenradius des Drehmeißels sollte beachtet werden, dass der Bogenradius der Schneide des Zweipunkt-Drehmeißels kleiner oder gleich dem minimalen Krümmungsradius an der konkaven Kontur des Teils sein sollte. Um Bearbeitungsstörungen zu vermeiden, sollte der Radius nicht zu klein gewählt werden, da er sonst nicht nur schwierig zu fertigen ist, sondern auch der Drehmeißel durch schwache Werkzeugspitzenfestigkeit oder schlechte Wärmeableitung des Werkzeugkörpers beschädigt wird.
3. Wählen Sie Werkzeuge zum CNC-Fräsen
In der CNC-Bearbeitung werden häufig Flachboden fräser zum Fräsen der Innen- und Außenkonturen von Planteilen und Fräsebenen verwendet. Die empirischen Daten der relevanten Parameter des Tools sind wie folgt:
1. Der Radius RD des Fräsers sollte kleiner sein als der minimale Krümmungsradius Rmin der Innenkonturfläche des Teils, im Allgemeinen RD = (0,8-0,9) Rmin.
2. Die Bearbeitungshöhe des Teils H< (1/4-1/6) RD, um eine ausreichende Steifigkeit des Messers zu gewährleisten.
3. Beim Fräsen des Grundes der inneren Nut mit einem Flachboden fräser. Da die beiden Durchgänge am Nutgrund überlappt werden müssen und der effektive Radius der Unterkante des Werkzeugs Re=Rr ist, d. h. der Durchmesser ist d=2Re=2 (Rr), und der Werkzeugradius ist Re=0,95 (Rr) während der Programmierung. Für die Bearbeitung einiger dreidimensionaler Profile und Konturen mit variablen Fasenwinkeln werden häufig Kugelfräser, Ring fräser, Trommel fräser, Kegelfräser und Scheiben fräser verwendet.
Die meisten CNC-Werkzeugmaschinen verwenden serialisierte und standardisierte Werkzeuge. Für die Werkzeugaufnahmen und -köpfe von Wendeschneidplatten-Außendreh werkzeugen und Plandreh werkzeugen gibt es nationale Normen und Serienmodelle. Für Bearbeitungszentren und Werkzeugmaschinen mit automatischem Werkzeugwechsler wurden Werkzeughalter serialisiert und standardisiert: Beispielsweise lautet der Standardcode des Kegelschaft werkzeug systems TSG-JT und der Standardcode des Zylinderschaft werkzeug systems ist DSG-JZ. Außerdem ist für das ausgewählte Werkzeug eine genaue Messung der Werkzeuggröße erforderlich, um vor der Verwendung genaue Daten zu erhalten. Der Bediener gibt diese Daten in das Daten system ein und schließt den Bearbeitungsprozess durch Aufruf des Programms ab, wodurch qualifizierte Werkstücke bearbeitet werden.
Daher muss zu Beginn der Programmausführung die Position bestimmt werden, an der sich das Werkzeug im Werkstück koordinatensystem zu bewegen beginnt. Diese Position ist der Startpunkt des Werkzeugs relativ zum Werkstück bei der Abarbeitung des Programms und wird daher als Programm startpunkt oder Startpunkt bezeichnet. Dieser Startpunkt wird im Allgemeinen durch die Werkzeugeinstellung bestimmt, daher wird dieser Punkt auch als Werkzeug einstellung punkt bezeichnet. Beim Übersetzen des Programms muss die Position des Werkzeug messpunktes richtig gewählt werden. Das Prinzip des Werkzeug einstell punktes ist: Erleichtern Sie die numerische Verarbeitung und vereinfachen Sie die Programmierung. Leicht auszurichten und während der Verarbeitung leicht zu überprüfen; Der verursachte Verarbeitungsfehler ist gering. Der Werkzeug einstell punkt kann am bearbeiteten Teil, aber auch an der Vorrichtung oder an der Werkzeugmaschine gesetzt werden. Um die Bearbeitung genauigkeit der Teile zu verbessern, sollte der Werkzeugeinstellpunkt möglichst auf den Konstruktions- oder Prozess nullpunkt des Teils gesetzt werden.
Im realen Betrieb der Werkzeugmaschine kann der Werkzeug positionspunkt des Werkzeugs durch manuellen Werkzeug einstell vorgang auf den Werkzeug messpunkt gelegt werden: Das heißt, die Übereinstimmung von "Werkzeug positionspunkt" und "Werkzeugeinstellpunkt". Der sogenannte "Werkzeug lagepunkt" bezieht sich auf den Positionierungs-Nullpunkt des Werkzeugs, und der Werkzeug lagepunkt des Drehmeißels ist die Werkzeugspitze bzw. der Mittelpunkt des Werkzeugspitzenbogens. Der Schaftfräser mit flachem Boden ist der Schnittpunkt der Werkzeugachse und der Unterseite des Werkzeugs, der Kugelfräser ist der Mittelpunkt der Kugel und der Bohrer ist die Spitze. Bei Verwendung des manuellen Werkzeug einstellbetriebs ist die Werkzeug einstell genauigkeit gering und die Effizienz gering. Einige Fabriken verwenden optische Werkzeug Einstellspiegel, Werkzeug Einstell Instrumente, automatische Werkzeugeinstellgeräte usw., um die Werkzeugeinstellzeit zu reduzieren und die Werkzeug einstell genauigkeit zu verbessern. Wenn das Werkzeug während der Bearbeitung gewechselt werden muss, sollte der Werkzeugwechselpunkt angegeben werden. Der sogenannte "Werkzeugwechselpunkt" bezeichnet die Position des Werkzeughalters, wenn dieser zum Werkzeugwechsel gedreht wird. Der Werkzeugwechselpunkt sollte sich außerhalb des Werkstücks oder der Vorrichtung befinden und das Werkstück und andere Teile dürfen beim Werkzeugwechsel nicht berührt werden.
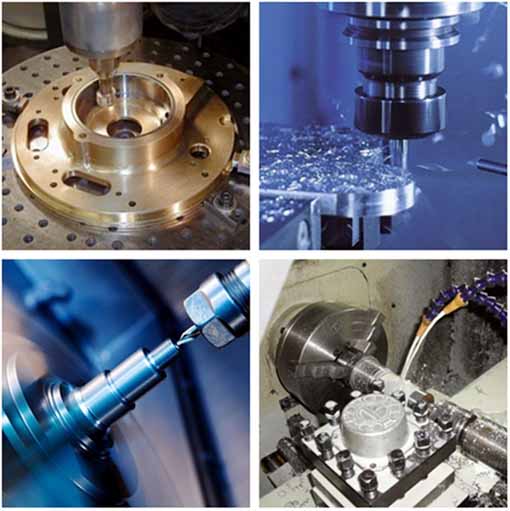
Grundlegende Definition der CNC-Bearbeitung
Die numerische Steuerung verarbeitung bezieht sich auf den vom Steuerungssystem ausgegebenen Befehl, um das Werkzeug verschiedene Bewegungen ausführen zu lassen, die den Anforderungen entsprechen. In Form von Zahlen und Buchstaben wird die von den technischen Anforderungen geforderte Bearbeitung und Bearbeitungs erfordernisse wie Form und Größe des Werkstücks ausgedrückt. Es bezieht sich im Allgemeinen auf den Prozess der Bearbeitung von Teilen auf CNC-Werkzeugmaschinen.Eine CNC-Werkzeugmaschine ist eine von einem Computer gesteuerte Werkzeugmaschine Der Computer, der zur Steuerung der Werkzeugmaschine verwendet wird, sei es ein Spezialcomputer oder ein Allzweckcomputer, wird zusammenfassend als CNC-System bezeichnet. Die Bewegungen und Hilfsaktionen der CNC-Werkzeugmaschine werden durch die Anweisungen des CNC-Systems gesteuert. Die Anweisungen der numerischen Steuerung werden vom Programmierer entsprechend dem Material des Werkstücks, den Bearbeitungsanforderungen, den Eigenschaften der Werkzeugmaschine und dem vom System vorgegebenen Anweisung format (numerische Steuersprache oder Symbole) zusammengestellt. Das numerische Steuersystem sendet Betriebs- oder Beendigung informationen an die Servovorrichtung und andere Funktion komponenten gemäß den Programm anweisungen, um verschiedene Bewegungen der Werkzeugmaschine zu steuern. Wenn das Teilebearbeitung programm endet, stoppt die Werkzeugmaschine automatisch. Bei jeder Art von CNC-Werkzeugmaschine kann die CNC-Werkzeugmaschine nicht arbeiten, wenn in ihrem CNC-System keine Programmbefehlseingabe vorhanden ist. Zu den gesteuerten Aktionen der Werkzeugmaschine gehören grob das Starten und Stoppen der Werkzeugmaschine; Spindelstart und -stopp, Drehrichtungs- und Drehzahländerung; Richtung, Geschwindigkeit und Modus der Vorschub bewegung; Werkzeugauswahl, Längen- und Radiuskorrektur; Werkzeugwechsel, Kühlmittel öffnen und schließen, etc.
Die Entwicklungsgeschichte der CNC-Technologie
Numerische Steuerungstechnik entstand aus den Bedürfnissen der Luftfahrtindustrie und wurde Ende der 1940er Jahre von einem US-Hubschrauberunternehmen vorgeschlagen. Als Ursprungsidee für CNC-Werkzeugmaschinen entwickelte das Massachusetts Institute of Technology 1952 eine dreiachsige CNC-Fräsmaschine. Diese Art von CNC-Fräsmaschine wurde Mitte der 1950er Jahre zur Bearbeitung von Flugzeugteilen eingesetzt. In den 1960er Jahren wurden die numerische Steuerung und die Programmierarbeit immer ausgereifter und perfekter. CNC-Werkzeugmaschinen wurden in verschiedenen Industriebereichen eingesetzt, aber die Luft- und Raumfahrtindustrie war schon immer der größte Anwender von CNC-Werkzeugmaschinen. Einige große Luftfahrtfabriken sind mit Hunderten von CNC-Werkzeugmaschinen ausgestattet, von denen Fräs- und Bohrmaschinen die wichtigsten sind. Die von CNC bearbeiteten Teile sind integrale Wandpaneele, Träger, Schotte und Propeller von Flugzeugen und Raketen; Die Formhohlräume des Gehäuses, der Welle, der Scheibe und der Schaufeln von Flugtriebwerken und der Hohlraum der Brennkammer des Flüssigkeitsraketentriebwerks usw. Die Anfangsphase der Entwicklung von CNC-Werkzeugmaschinen basiert auf CNC-Werkzeugmaschinen mit kontinuierlicher Trajektorie und kontinuierlicher Trajektorien steuerung.Die kontinuierliche Bahnsteuerung wird auch als Kontursteuerung bezeichnet, die erfordert, dass sich das Werkzeug auf einer vorgegebenen Bahn relativ zum Teil bewegt. Später werden wir energisch punktgesteuerte CNC-Werkzeugmaschinen entwickeln. Punktsteuerung bedeutet, dass sich das Werkzeug von einem Punkt zum anderen bewegt, solange es das Ziel am Ende genau erreichen kann, unabhängig von der Bewegungsroute.
Der Betriebsprozess der CNC-Bearbeitung
NC-ProgrammierungFür die NC-Bearbeitung programmierung gibt es manuelle (manuelle) Programmierung und automatische Programmierung methoden. Manuelle Programmierung, der gesamte Inhalt des Programms wird gemäß dem vom CNC-System vorgegebenen Anweisung format manuell geschrieben. Automatische Programmierung ist Computer programmierung, die in automatische Programmier methoden basierend auf Sprache und Zeichnung unterteilt werden kann. Unabhängig von der Art des automatischen Programmieren verfahrens ist jedoch entsprechende Hard- und Software erforderlich.
Es zeigt sich, dass die Umsetzung der CNC-Bearbeitung programmierung der Schlüssel ist. Aber Programmieren allein reicht nicht aus: Zur CNC-Bearbeitung gehören auch eine Reihe von Vorarbeiten, die vor der Programmierung und nach der Programmierung zu erledigen sind. Im Allgemeinen sind die Hauptinhalte des CNC-Bearbeitung prozesses wie folgt:
⑴ Wählen und bestätigen Sie die Teile und Inhalte für die CNC-Bearbeitung;
⑵ Prozessanalyse der CNC-Bearbeitung von Teile zeichnungen;
⑶ Prozessgestaltung der CNC-Bearbeitung;
⑷ Mathematische Bearbeitung von Teilezeichnungen;
⑸ Erstellen Sie die Liste der Verarbeitungsverfahren;
⑹ Stellen Sie das Kontroll medium gemäß der Verfahrensliste her;
⑺ Überprüfen und ändern Sie das Programm;
⑻ Probe bearbeitung von Prototypen und Problem behandlung vor Ort;
⑼ Erstellung und Ablage von CNC-Bearbeitung prozess dokumenten.
Um den Automatisierungsgrad der Produktion zu verbessern, die Programmierzeit zu verkürzen und die Kosten der CNC-Bearbeitung zu senken, wurden eine Reihe fortschrittlicher CNC-Bearbeitung technologien entwickelt und in der Luft- und Raumfahrtindustrie eingesetzt. B. eine numerische Computersteuerung, das heißt, ein Klein- oder Mikrocomputer wird verwendet, um die Steuerung in dem numerischen Steuerung system zu ersetzen, und die im Computer gespeicherte Software wird verwendet, um Berechnungs- und Steuerfunktionen auszuführen. Diese Art von Soft-Connected-Computer-Numerical-Control-System ersetzt nach und nach das Numerical-Control-System im Anfangszustand. Direkte numerische Steuerung bedeutet, einen Computer zu verwenden, um mehrere numerisch gesteuerte Werkzeugmaschinen direkt zu steuern, was für die Kleinserien- und Kurztakt produktion von Flugzeugen sehr geeignet ist. Das ideale Steuersystem ist ein adaptives Steuersystem, das Verarbeitungsparameter kontinuierlich ändern kann.Obwohl das System selbst komplex und teuer ist, kann es die Verarbeitung effizienz und -qualität verbessern. Neben der hardwaremäßigen Verbesserung von CNC-Systemen und Werkzeugmaschinen hat die CNC-Entwicklung einen weiteren wichtigen Aspekt, nämlich die Entwicklung von Software. Computergestützte Programmierung (auch automatische Programmierung genannt) bedeutet, dass, nachdem ein Programmierer ein Programm in numerischer Steuerung sprache geschrieben hat, dieses zur Übersetzung in den Computer eingegeben wird und der Computer es schließlich automatisch ausgibt. Die am weitesten verbreitete CNC-Sprache ist die APT-Sprache. Es gliedert sich grob in ein Haupt bearbeitung programm und ein Nach bearbeitung programm. Ersteres übersetzt das vom Programmierer geschriebene Programm und berechnet die Werkzeugbahn;Letzterer übersetzt die Werkzeugbahn in ein Teile bearbeitung programm einer CNC-Werkzeugmaschine.
Numerische Steuerung verarbeitung besteht darin, ein Programm auf den Computer zu schreiben, bevor das Werkstück verarbeitet wird. Geben Sie diese Programme dann in die Werkzeugmaschine ein, die von dem Computerprogramm zur Befehlsverarbeitung gesteuert wird. Oder schreiben Sie direkt Anweisungen für die CNC-Bearbeitung auf dem von diesem Computerprogramm gesteuerten Bedienfeld der Werkzeugmaschine. Der Bearbeitungsprozess umfasst: Werkzeug vorschub, Werkzeugwechsel, Geschwindigkeit wechsel, Richtung wechsel, Stopp usw., die alle automatisch abgeschlossen werden. Die CNC-Bearbeitung ist eine fortschrittliche Methode der modernen Formenherstellung und -bearbeitung. Natürlich müssen CNC-Bearbeitungsverfahren nicht nur für die Formteilbearbeitung eingesetzt werden, sondern haben auch ein breites Einsatzspektrum.
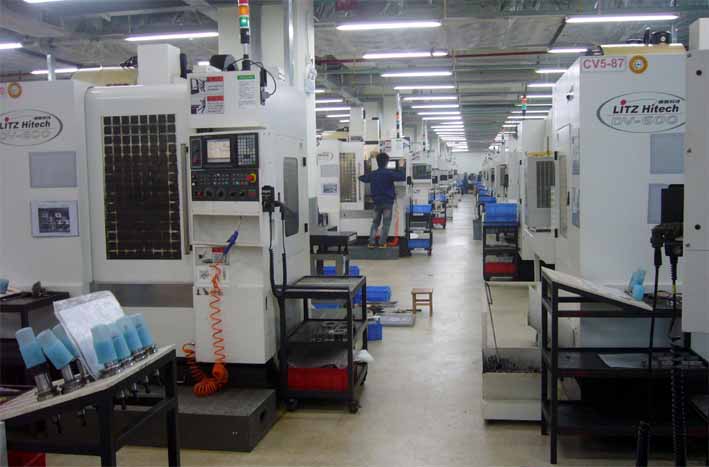
Prozessanalyse des Werkstücks
Die technischen Fragestellungen der CNC-Bearbeitung der bearbeiteten Teile umfassen vielfältige Aspekte. Das Folgende ist eine Kombination aus der Möglichkeit und dem Komfort der Programmierung, um einige Hauptinhalte vorzulegen, die analysiert und überprüft werden müssen.1. Die Dimensionierung sollte den Eigenschaften der CNC-Bearbeitung entsprechen
Bei der CNC-Programmierung basieren die Größe und Position aller Punkte, Linien und Flächen auf dem Programmier ursprung. Daher ist es am besten, die Koordinaten größe direkt in der Teilezeichnung anzugeben oder zu versuchen, die Größe mit demselben Bezugspunkt anzugeben.
2. Die Bedingungen der geometrischen Elemente sollten vollständig und genau sein
Bei der Programmierung muss der Programmierer die Parameter der geometrischen Elemente, die die Kontur des Teils und die Beziehung zwischen den geometrischen Elementen bilden, vollständig erfassen. Da bei der automatischen Programmierung alle geometrischen Elemente der Kontur des Teils definiert werden müssen, müssen bei der manuellen Programmierung die Koordinaten jedes Knotens berechnet werden. Egal welcher Punkt unklar oder ungewiss ist, eine Programmierung kann nicht durchgeführt werden. Aufgrund unzureichender Berücksichtigung oder Vernachlässigung durch Teile konstrukteure im Konstruktionsprozess gibt es jedoch oft unvollständige oder unklare Parameter wie Bogen und Gerade, Bogen und Bogen, unabhängig davon, ob sie tangential sind oder sich schneiden oder getrennt sind. Daher müssen Sie bei der Überprüfung und Analyse der Zeichnungen vorsichtig sein und sich rechtzeitig an den Konstrukteur wenden, wenn Sie Probleme feststellen.
3. Zuverlässige Positionierung referenz
In der CNC-Bearbeitung sind die Bearbeitungsprozesse oft konzentriert und es ist sehr wichtig, sie auf derselben Basis zu verorten. Daher ist es oft erforderlich, einige Hilfsbezugspunkte festzulegen oder einige Prozessvorsprünge auf dem Rohling hinzuzufügen.
4. Einheitlicher Geometrietyp oder -größe
Es ist am besten, einen einheitlichen geometrischen Typ oder eine einheitliche Größe für die Form und die innere Kavität des Teils zu verwenden, damit die Anzahl der Werkzeugwechsel reduziert und das Programm gesteuert werden kann, um die Länge des Programms zu verkürzen.
Die Form der Teile ist so symmetrisch wie möglich, was für die Programmierung mit der Spiegel bearbeitung funktion der CNC-Werkzeugmaschine praktisch ist, um Programmierzeit zu sparen.
Spannen von Teilen
1. Die Grundprinzipien der Positionierung und InstallationBei der Bearbeitung von Teilen auf einer CNC-Werkzeugmaschine besteht das Grundprinzip der Positionierung und Montage darin, einen sinnvollen Positionsbezug und Aufspannplan zu wählen. Achten Sie bei der Auswahl auf folgende Punkte:
1. Streben Sie nach einem einheitlichen Benchmark für Konstruktions-, Prozess- und Programmier berechnungen.
2. Minimieren Sie die Anzahl der Spannzeiten und bearbeiten Sie nach dem Positionieren und Spannen möglichst alle zu bearbeitenden Flächen einmal.
3. Vermeiden Sie die Verwendung von CNC-Bearbeitung schemata, die nach dem Herunterfahren manuell angepasst werden. Sollte die Effektivität von CNC-Werkzeugmaschinen voll ausspielen.
zwei, Grundprinzipien für die Auswahl von Vorrichtungen
Die Eigenschaften der CNC-Bearbeitung stellen zwei grundlegende Anforderungen an die Vorrichtung:
Eine besteht darin, sicherzustellen, dass die Koordinatenrichtung der Spannvorrichtung relativ zur Koordinatenrichtung der Werkzeugmaschine festgelegt ist;
Die zweite besteht darin, die Größenbeziehung zwischen den Teilen und dem Maschinen koordinatensystem zu koordinieren. Darüber hinaus sollten folgende Punkte beachtet werden:
1. Wenn die Teilecharge nicht groß ist, sollten so oft wie möglich modulare Vorrichtungen, verstellbare Vorrichtungen und andere allgemeine Vorrichtungen verwendet werden. Um die Produktionsvorbereitung zeit zu verkürzen und Produktionskosten zu sparen.
2. Berücksichtigen Sie bei der Massenproduktion nur die Verwendung spezieller Vorrichtungen und bemühen Sie sich um eine einfache Struktur.
3. Das Be- und Entladen von Teilen sollte schnell, bequem und zuverlässig sein, um die Maschinenstoppzeit zu verkürzen.
4. Die Teile auf der Vorrichtung dürfen die Bearbeitung der Oberflächen der Teile durch die Werkzeugmaschine nicht behindern, dh die Vorrichtung sollte geöffnet sein. Seine Positionierungs- und Klemm mechanismus komponenten können das Schneiden während der Bearbeitung (wie Kollision usw.) nicht beeinträchtigen.
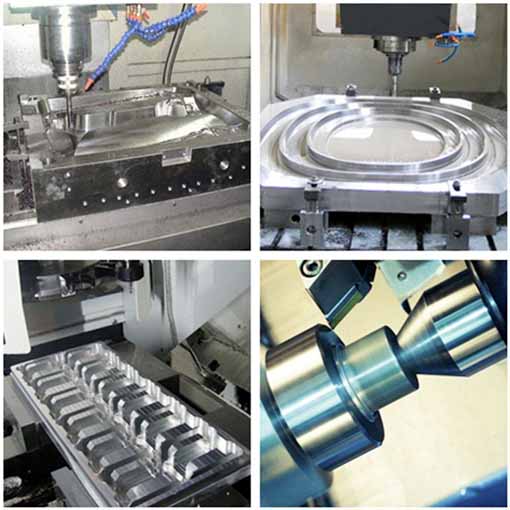
Bearbeitungsfehler
CNC-Bearbeitungsfehler △ Nummer:Es besteht aus Programmierfehler △ Bearbeitung, Werkzeug maschinen fehler △ Maschine, Positionier fehler △ behoben, Werkzeug einstellung fehler △ und anderen Fehlern.
Nämlich: △Zahl plus = f (△ Bearbeiten + △ Maschine + △ Fest + △ Messer)
in:
1. Programmierfehler △ setzt sich zusammen aus Näherungsfehler δ und Rundungsfehler. Der Approximations fehler δ entsteht bei der Approximation einer nicht kreisförmigen Kurve mit einem geraden Streckenabschnitt oder einem Kreisbogenabschnitt, wie in Abbildung 1.43 dargestellt. Der Rundungsfehler ist der Fehler, der durch Runden des Koordinaten werts auf einen ganzzahligen impuls äquivalenten Wert während der Daten verarbeitung erzeugt wird. Impuls äquivalent bezieht sich auf die Verschiebung jedes Einheitsimpulses entsprechend der Koordinatenachse. Normale Präzisions-CNC-Werkzeugmaschinen, der allgemeine Impuls äquivalen twert beträgt 0,01 mm; Der Puls äquivalent wert von präziseren CNC-Werkzeugmaschinen beträgt 0,005 mm oder 0,001 mm usw.
2. Der Fehler der Werkzeugmaschine wird durch den Fehler des CNC-Systems und des Vorschub systems verursacht.
3. Der Positionier fehler △ wird immer dann verursacht, wenn das Werkstück auf der Vorrichtung positioniert ist und die Vorrichtung auf der Werkzeugmaschine positioniert ist.
4. Werkzeug einstellung fehler △ Werkzeug wird bei der Bestimmung der relativen Position von Werkzeug und Werkstück erzeugt.
NC-Programmierung
ProgrammstrukturEin Programmsegment ist eine fortlaufende Wortgruppe, die als Einheit verarbeitet werden kann, und es ist eigentlich ein Abschnitt eines Programms in einem CNC-Bearbeitung programm. Der Hauptteil des Teile bearbeitung programms besteht aus mehreren Programm abschnitten. Die meisten Programm segmente werden verwendet, um die Werkzeugmaschine anzuweisen, eine bestimmte Aktion abzuschließen oder auszuführen. Der Programmteil ist: Es besteht aus Größen wörtern, Nicht größen wörtern und Blockende befehlen. Beim Schreiben und Drucken belegt jeder Block im Allgemeinen eine Zeile und das gleiche gilt, wenn das Programm auf dem Bildschirm angezeigt wird.
Programm-Format
Ein konventionelles CNC-Bearbeitung programm besteht aus Startsymbol (einzelne Zeile), Programmname (einzelne Zeile), Programm rumpf und Programmende anweisung (im Allgemeinen einzeilig). Am Ende des Programms steht ein Programmende zeichen. Das Programmstartzeichen und das Programmende zeichen sind die gleichen Zeichen: % im ISO-Code, ER im EIA-Code. Der Programmende befehl kann M02 (Programmende) oder M30 (Papier bandende) sein. CNC-Werkzeugmaschinen verwenden im Allgemeinen gespeicherte Programme zum Ausführen.Zu diesem Zeitpunkt sind die gemeinsamen Punkte von M02 und M30: Nach Beendigung aller anderen Befehle im Satz werden Spindel, Kühlmittel und Vorschub gestoppt und die Steuerung zurückgesetzt. M02 und M30 sind bei einigen Werkzeugmaschinen (Systemen) völlig gleichwertig, während die folgenden Unterschiede bei anderen Werkzeugmaschinen (Systemen) verwendet werden: Wenn das Programm mit M02 beendet wird, stoppt der Cursor am Ende des Programms, nachdem der Automatikbetrieb beendet ist; Bei Verwendung von M3O zum Beenden des Programm betriebs können die Cursor- und Bildschirmanzeige nach Beendigung des Automatikbetriebs automatisch zum Anfang des Programms zurückkehren und das Programm kann durch Drücken der Starttaste erneut ausgeführt werden. Obwohl M02 und M30 einen Block mit anderen Programm wörtern teilen dürfen, ist es besser, sie in einem einzigen Block aufzulisten oder einen Block nur mit der Sequenznummer zu teilen.
Der Programmname steht vor dem Hauptteil des Programms und nach dem Programmstart und nimmt normalerweise eine eigene Zeile ein. Der Programmname hat zwei Formen: Einer besteht aus vorgeschriebenen englischen Zeichen (normalerweise O), gefolgt von mehreren Ziffern. Die maximal zulässige Anzahl von Stellen ist im Handbuch festgelegt, und die beiden gebräuchlichen sind zweistellig und vierstellig. Diese Form des Programmnamens kann auch als Programmnummer bezeichnet werden. Eine andere Form besteht darin, dass der Programmname aus englischen Zeichen, Zahlen oder einer Mischung aus Englisch und Zahlen besteht und in der Mitte ein „-“-Zeichen hinzugefügt werden kann. Dieses Formular macht das Verfahren der Benutzer Umbenennen flexibler. Das Programm für den dritten Bearbeitung vorgang des Flansches mit der Teilezeichnung nummer 215 auf der CNC-Drehmaschine LC30 kann beispielsweise LC30-FIANGE-215-3 heißen. Dies bringt großen Komfort bei Verwendung, Lagerung und Abruf. Die Form des Programmnamens wird vom CNC-System bestimmt.
%
O1001
N0 G92 X0 Y0 Z0
N5 G91 G00 X50 Y35 S500 MO3
N10 G43 Z-25 T01.01
N15 G01 G007 Z-12
N20 G00 Z12
N25 X40
N30 G01 Z-17
N35 G00 G44 Z42 M05
N40 G90 X0 Y0
N45 M30
%
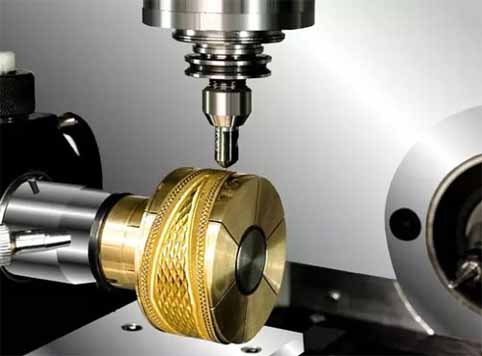
Segment-Format
Die Regeln für die Anordnung von Wörtern, Zeichen und Daten in einem Programm abschnitt werden als Block format bezeichnet. Das feste Sequenz format und das Trennzeichen format (HT oder TAB) wurden in der Geschichte der CNC verwendet. Wenn diese beiden Programm segment formate bestanden sind, wird das variable Programm segment format der Wortadresse im In- und Ausland weit verbreitet verwendet, auch als Wort adressen format bekannt. Bei diesem Format ist die Programm wortlänge nicht fest und auch die Anzahl der Programmworte ist variabel.Die meisten CNC-Systeme erlauben eine beliebige Anordnung der Programm wortreihenfolge, sie gehört also zum variablen Satz format. In den meisten Fällen werden jedoch zur Vereinfachung des Schreibens, Eingebens, Prüfens und Korrekturlesens Programm wörter verwendet, um im Programm segment in einer bestimmten Reihenfolge anzuordnen. Das Programmierhandbuch der CNC-Werkzeugmaschine verwendet ein detailliertes Format, um die Details der Programm ierung zu klassifizieren und festzulegen: Die bei der Programm ierung verwendeten Zeichen, die Reihenfolge und Wortlänge der Programm wörter im Programm segment usw. Z.B:
/ NO3 G02 X+053 Y+053 I0 J+053 F031 S04 T04 M03 LF
Die detaillierte Format klassifizierung des obigen Beispiels sieht wie folgt aus: N03 ist die Sequenznummer des Programm segments; G02 bedeutet, dass die Bearbeitung spur ein Bogen im Uhrzeigersinn ist; X+053, Y+053 geben die Koordinaten des Endpunkts des zu bearbeitenden Bogens an; I0, J+053 stellen die Mittelpunkt koordinaten des zu verarbeitenden Bogens dar; F031 ist die Vorschubgesch windigkeit der CNC-Bearbeitung; S04 ist die Spindeldrehzahl; T04 ist die Werkzeugnummer des verwendeten Werkzeugs; M03 ist ein Hilfsfunktion befehl; LF-Blockende-Befehl; / ist ein Sprungau wahl befehl. Die Funktion des Auswahl befehls überspringen ist: Unter der Prämisse, dass das Programm unverändert bleibt, kann der Bediener wählen, ob er die Blöcke im Programm mit Anweisungen zum Überspringen der Auswahl ausführen möchte oder nicht. Die Auswahlmethode besteht in der Regel darin, den Auswahlschalter zum Überspringen auf dem Maschinen bedienfeld auf ON oder OFF zu stellen, um die Nichtausführung oder die Ausführung des Satzes mit "/" zu realisieren.
Programm ausführen
Diese Situation tritt manchmal beim Kompilieren eines CNC-Bearbeitung programms auf: Eine Gruppe von Programm segmenten kommt in einem Programm mehrfach vor oder muss in mehreren Programmen verwendet werden. Wir können diese Gruppe von Programm segmenten extrahieren, benennen und separat speichern, diese Gruppe von Programm segmenten sind Unterprogramme. Ein Unterprogramm ist ein Abschnitt eines Verarbeitung programms, das durch entsprechende Maschinen steuerung befehle aufgerufen werden kann, und hat im Allgemeinen eine unabhängige Bedeutung bei der Verarbeitung. Das Verarbeitung programm, in dem sich die Anweisung zum Aufrufen des Unterprogramms der ersten Ebene befindet, wird als Hauptprogramm bezeichnet. Der Befehl zum Anpassen des Unterprogramms ist auch ein Programm abschnitt, der im Allgemeinen aus dem Unterprogrammaufruf befehl, dem Namen des Unterprogramms und der Anzahl der Aufrufe besteht. Die spezifischen Regeln und Formate variieren von System zu System, zum Beispiel ist es auch „unterprogramm Nr. 55 einmal aufrufen“, das FANUC-System verwendet „M98 P55.“ und das amerikanische A-B-Firmensystem verwendet „P55x“.
Unterprogramme können verschachtelt werden, dh Schicht für Schicht. Die Beziehung zwischen der oberen Ebene und der nächsten Ebene ist dieselbe wie die Beziehung zwischen dem Hauptprogramm und dem Unterprogramm der ersten Ebene. Die maximal einstellbare Lagenanzahl hängt vom jeweiligen CNC-System ab. Form und Aufbau des Unterprogramms entsprechen in etwa dem Hauptprogramm: Die erste Zeile ist die Unter programmnummer (Name), die letzte Zeile ist die Anweisung "Unter programmende" und dazwischen der Unter programm rumpf. Die Funktion der Hauptprogramm-Ende-Anweisung besteht jedoch darin, das Hauptprogramm zu beenden und das CNC-System zurückzusetzen. Seine Anweisungen wurden standardisiert und alle Systeme verwenden M02 oder M30; Und die Funktion des Unterprogramm-Ende-Befehls besteht darin, das Unterprogramm zu beenden, zum Hauptprogramm oder dem Unterprogramm der höheren Ebene zurückzukehren. Die Befehle sind in verschiedenen Systemen nicht einheitlich, wie M99 für das FANUC-System, M17 für das Siemens-System, M02 für das System der amerikanischen A-B-Firma usw.
Benutzermakros (Programme) können in CNC-Bearbeitung programmen verwendet werden. Das sogenannte Makroprogramm ist ein Unterprogramm, das Variablen enthält. Der Befehl, der das Makroprogramm im Programm aufruft, wird als Benutzer makrobefehl bezeichnet, und die Funktion, die das System mit dem Benutzermakro programm verwenden kann, wird als Benutzermakro funktion bezeichnet. Bei der Ausführung müssen Sie nur den Benutzer makrobefehl schreiben, um seine Benutzermakro funktion auszuführen.
Die größten Funktionen von Benutzermakros sind:
● Variablen können in Benutzermakros verwendet werden;
● Sie können Berechnung formeln, Steuerung anweisungen und verschiedene Funktionen verwenden
● Sie können Benutzer makrobefehle verwenden, um Variablen Werte zuzuweisen.
Die CNC-Werkzeugmaschine verwendet Gruppen technologie zur Bearbeitung von Teilen, wodurch die Losgröße erweitert, der Programmier aufwand reduziert und die Wirtschaftlichkeit verbessert werden kann. Bei der Gruppen bearbeitung werden die Teile klassifiziert und das Bearbeitung programm für diese Art von Teilen kompiliert, anstatt für jedes Teil ein Programm zu editieren. Bei der Verarbeitung der gleichen Art von Teilen mit unterschiedlichen Größen besteht der Hauptvorteil der Verwendung von Benutzermakros darin, dass Variablen anstelle von bestimmten Werten verwendet werden können. Wenn es um die eigentliche Verarbeitung geht, weisen Sie der Variablen einfach den tatsächlichen Größenwert dieses Teils mit dem Benutzer makrobefehl zu.
Prinzipien der CNC-Bearbeitung
⑴ Die Bearbeitung des vorherigen Prozesses hat keinen Einfluss auf das Positionieren und Spannen des nächsten Prozesses.
⑵ Zuerst innen, dann außen, dh zuerst wird die innere Kavität (inneres Loch) und dann die äußere Form bearbeitet.
⑶ Der Bearbeitungsprozess mit der gleichen Anlage oder mit dem gleichen Werkzeug sollte kontinuierlich durchgeführt werden, um Fehler durch Neu positionierung oder Werkzeugwechsel zu reduzieren.
⑷ In der gleichen Anlage sollte zuerst der Vorgang durchgeführt werden, der wenig Einfluss auf die Steifigkeit des Werkstücks hat.

Bearbeitungsweg
Die Bearbeitung strecke Vorschub der CNC-Drehmaschine bezeichnet den Weg, den das Drehwerkzeug vom Werkzeugeinstellpunkt (bzw. dem festen Nullpunkt der Werkzeugmaschine) bis zu diesem Punkt zurückfährt und das Bearbeitung programm beendet. Inklusive Schnittwege und spanlose Leerwege wie Schneiden und Ausschneiden durch das Werkzeug.
Der Vorschub weg beim Schlichten erfolgt grundsätzlich entlang der Teile konturfolge. Daher liegt der Schwerpunkt bei der Bestimmung der Vorschub route auf der Bestimmung der Vorschub route für die Schrupp bearbeitung und den Leerhub.
Bei der CNC-Drehmaschinen bearbeitung folgt die Bestimmung der Bearbeitung route im Allgemeinen den folgenden Prinzipien.
① Sie sollte die Genauigkeit und Oberflächenrauheit des zu bearbeitenden Werkstücks gewährleisten können.
② Machen Sie den Verarbeitung weg so kurz wie möglich, reduzieren Sie die Leerlaufzeit und verbessern Sie die Verarbeitung effizienz.
③ Versuchen Sie, den Arbeitsaufwand bei der numerischen Berechnung zu vereinfachen und den Verarbeitung prozess zu vereinfachen.
④ Für einige wiederverwendbare Programme sollten Unterprogramme verwendet werden.
Machen Sie das Verarbeitung programm über den kürzesten Vorschub weg, können Sie nicht nur die Ausführungszeit des gesamten Verarbeitung prozesses einsparen. Es kann auch unnötigen Werkzeugverbrauch und Verschleiß der gleitenden Teile des Vorschub mechanismus der Werkzeugmaschine reduzieren. Die Typen und Implementierung methoden der kürzesten Feedroute sind wie folgt:
⑴ Der kürzeste Schnitt vorschub weg. Der kürzeste Schnitt vorschub weg kann die Produktionseffizienz effektiv verbessern und den Werkzeugverlust reduzieren. Bei der Gestaltung des kürzesten Schnitt vorschub weges ist auch auf die Steifigkeit des Werkstücks und die bearbeitung technischen Anforderungen zu achten.
⑵ Die kürzeste Leerfahrtroute.
① Den Ausgangspunkt der Bearbeitung geschickt nutzen.
Ein Beispiel für eine allgemeine Situation beim Schruppen im Rechteck schleifenmodus. Die Einstellung der Werkzeugspitze A soll der Notwendigkeit eines bequemen Werkzeugwechsels bei der Schlichtbearbeitung und anderen Bearbeitung prozessen Rechnung tragen, so dass sie weit vom Rohling entfernt liegt. Gleichzeitig den Startpunkt mit dem Werkzeugeinstellpunkt abgleichen
② Stellen Sie den CNC-Werkzeugwechselpunkt geschickt ein.
Um den Komfort und die Sicherheit des Werkzeugwechsels zu berücksichtigen, wird der Werkzeugwechselpunkt manchmal auch weit vom Rohling entfernt gesetzt. Dann wird beim Wechsel des zweiten Messers der Leerweg beim Feindrehen zwangsläufig länger; Wird der Werkzeugwechselpunkt des zweiten Werkzeugs ebenfalls auf die Nicht-Punkt-Position in der Mitte gesetzt, kann die Leerhubstrecke verkürzt werden.
③ Die CNC-Route "Rückkehr auf Null" sinnvoll gestalten. Um den Berechnung prozess zu vereinfachen und die Überprüfung beim manuellen Erstellen des Bearbeitung programms der komplexen Kontur zu erleichtern, führt der Programmierer manchmal nach jeder Bearbeitung die Operation "Rückkehr auf Null" für den Endpunkt des Werkzeugs aus. Lassen Sie alles an die Position des Werkzeu geinstell punktes zurückkehren und führen Sie dann das nachfolgende Programm aus. Dies erhöht den Abstand des Zufuhrpfads und verringert die Produktion effizienz. Daher sollte bei einer rationellen Anordnung der Route "Zurück zu Null" der Abstand zwischen dem Endpunkt des vorherigen Schnitts und dem Startpunkt des nächsten Schnitts so kurz wie möglich sein. Oder Null, um die Anforderung des kürzesten Vorschubwegs zu erfüllen. Verwenden Sie außerdem bei der Auswahl des Befehls zum Zurückkehren zum Werkzeugeinstellpunkt unter der Voraussetzung, dass keine Störung vorliegt, den bidirektionalen Befehl "Rückkehr auf Null" der x- und z-Achse so oft wie möglich gleichzeitig. Der Weg der Funktion "zurück auf Null" ist der kürzeste.
⑶ Schritt CNC-Schneid vorschubweg des Rohlings mit großem Rand. Es werden zwei Schnittvorschub wege für Zuschnitte mit zu viel Rand aufgelistet. Es ist der falsche Schritt-Schneidweg: Schneiden in der Reihenfolge von 1 Eimer und 5, der verbleibende Rand für jeden Schnitt ist gleich, was der richtige Schritt-Schneid vorschubweg ist. Denn unter gleicher Schnittstärke.
⑷ Kontinuierlicher Schnittvorschubweg für die Schlichtteilkontur. Das Schlichten der Kontur des Teils kann mit einem oder mehreren Schlichtvorgängen erfolgen. Die fertige Kontur soll durch den letzten Schnitt kontinuierlich bearbeitet werden. Zu diesem Zeitpunkt sollten die Vorwärts- und Rückwärtspositionen des Werkzeugs geeignet ausgewählt werden. Versuchen Sie, Schnitt und Schnitt bzw. Werkzeugwechsel und Pause nicht in einer kontinuierlichen Kontur anzuordnen, um das Gleichgewicht des Prozesssystems nicht durch plötzliche Schnittkraftänderungen zu beschädigen. Verursachen Sie Kratzer, Formmutationen oder bleibende Werkzeugspuren auf der Kontur des Teils.
⑸ Spezieller Zuführungsweg. In der CNC-Drehbearbeitung unter normalen Umständen. Der Längsvorschub des Werkzeugs erfolgt in negativer Richtung der Koordinate, aber manchmal ist es nicht sinnvoll, den Vorschubweg entsprechend seiner normalen negativen Richtung anzuordnen. Es kann sogar das Werkstück beschädigen.
Vor-und Nachteile
Die CNC-Bearbeitung hat folgende Vorteile:① Die Anzahl der Werkzeuge wird stark reduziert und komplexe Werkzeuge sind für die Bearbeitung von Teilen mit komplexen Formen nicht erforderlich. Wenn Sie die Form und Größe des Teils ändern möchten, müssen Sie nur das Teilebearbeitungsprogramm ändern, das für die Entwicklung und Modifikation neuer Produkte geeignet ist.
② Die Bearbeitungsqualität ist stabil, die Bearbeitungsgenauigkeit ist hoch und die Wiederholgenauigkeit ist hoch, was für die Bearbeitungsanforderungen von Flugzeugteilen geeignet ist.
③ Bei der Mehrsorten- und Kleinserienfertigung ist die Produktionseffizienz höher, was die Zeit für die Produktionsvorbereitung, die Werkzeugmaschineneinstellung und die Prozessinspektion verkürzen kann, und die Schnittzeit wird durch die Verwendung der besten Schnittmenge reduziert .
④ Es kann komplexe Oberflächen bearbeiten, die mit herkömmlichen Methoden schwer zu bearbeiten sind, und sogar einige unbeobachtbare Bearbeitungsteile bearbeiten. Der Nachteil der CNC-Bearbeitung besteht darin, dass die Werkzeugmaschinen teuer sind und ein hohes Maß an Wartungspersonal erfordern.
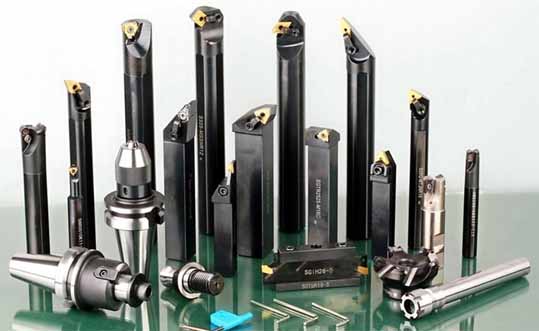
Auswahl von CNC-Werkzeugen
1. Das Prinzip der Auswahl von CNC-WerkzeugenDie Standzeit hängt eng mit dem Zerspanvolumen zusammen. Bei der Formulierung von Schnittparametern sollte zunächst die sinnvolle Standzeit gewählt und die sinnvolle Standzeit entsprechend dem Optimierungsziel ermittelt werden. Im Allgemeinen unterteilt in die Werkzeugstandzeit mit der höchsten Produktivität und die Werkzeugstandzeit mit den niedrigsten Kosten. Ersteres wird nach dem Ziel der geringsten Einzelstück-Mannstunden und letzteres nach dem Ziel der niedrigsten Prozesskosten bestimmt.
Bei der Wahl der Standzeit können Sie je nach Komplexität des Werkzeugs, Fertigungs- und Schleifkosten folgende Punkte berücksichtigen. Die Standzeit von komplexen und hochpräzisen Werkzeugen sollte höher gewählt werden als die von einschneidigen Werkzeugen. Bei Wendeschneid werkzeugen mit Maschinenklemmung kann aufgrund der kurzen Werkzeugwechselzeit, um die Schneidleistung voll auszuschöpfen und die Produktionseffizienz zu verbessern, die Werkzeugstandzeit niedriger gewählt werden, in der Regel 15-30 Minuten. Bei Multitools, modularen Werkzeug maschinen und automatisierten Bearbeitung werkzeugen mit komplexer Werkzeug installation, Werkzeugwechsel und Werkzeug einstellung soll die Standzeit höher sein und insbesondere die Zuverlässigkeit des Werkzeugs gewährleistet sein. Wenn die Produktivität eines bestimmten Prozesses in der Werkstatt die Verbesserung der Produktivität der gesamten Werkstatt begrenzt, sollte die Werkzeugstandzeit des Prozesses niedriger gewählt werden. Bei großen Kosten der Gesamtanlage, die sich auf eine bestimmte Prozesseinheit Zeit teilen, sollte auch die Werkzeugstandzeit geringer gewählt werden. Um beim Schlichten großer Teile sicherzustellen, dass mindestens ein Durchgang abgeschlossen ist und das Werkzeug nicht mitten im Schnitt gewechselt wird, sollte die Standzeit entsprechend der Genauigkeit des Teils und der Oberflächenrauheit bestimmt werden. Im Vergleich zu herkömmlichen Werkzeug maschinen bearbeitung verfahren stellt die CNC-Bearbeitung höhere Anforderungen an die Zerspanungswerkzeuge. Es muss nicht nur steif und hochpräzise sein, sondern erfordert auch stabile Abmessungen, hohe Lebensdauer und gleichzeitig einfache Montage und Einstellung für die Brech- und Austragsleistung, um den hohen Effizienzanforderungen von CNC-Werkzeugmaschinen gerecht zu werden. Die ausgewählten Werkzeuge auf CNC-Werkzeugmaschinen verwenden häufig hoch geschwindigkeit geeignete Werkzeug materialien (z. B. Schnellarbeitsstahl, Feinstkorn-Hartmetall) und verwenden Wendeschneidplatten.
2. Wählen Sie Werkzeuge zum CNC-Drehen
Die gebräuchlichen CNC-Dreh werkzeuge werden im Allgemeinen in drei Typen unterteilt: Umform Drehen werkzeuge, Spitz Drehen werkzeuge, Bogen drehwerkzeuge und drei Typen. Umformende Drehwerkzeuge werden auch Prototypen drehwerkzeuge genannt, und die Konturform der bearbeiteten Teile wird vollständig durch die Form und Größe der Schneidkante des Drehwerkzeugs bestimmt. In der CNC-Drehbearbeitung umfassen gängige Umform drehwerkzeuge Bogen drehwerkzeuge mit kleinem Radius, nicht rechteckige Drehwerkzeuge und Gewindewerkzeuge. Bei der CNC-Bearbeitung sollte das Umform drehwerkzeug so wenig wie möglich eingesetzt werden oder nicht. Der Spitzdrehmeißel ist ein Drehmeißel, der sich durch eine gerade Schneide auszeichnet. Die Spitze dieses Drehmeißeltyps besteht aus linearen Haupt- und Nebenschneiden: Zum Beispiel 900 Innen- und Außendreh werkzeuge, linke und rechte Stirndrehwerkzeuge, Stech- (Schneid-)Drehwerkzeuge und verschiedene Außen- und Innendrehwerkzeuge mit sehr kleinen Spitzenfasen.
Die Auswahl der geometrischen Parameter des spitzen Drehwerkzeugs (hauptsächlich des geometrischen Winkels) ist im Wesentlichen die gleiche wie beim gewöhnlichen Drehen: Die Eigenschaften der CNC-Bearbeitung (wie Bearbeitung route, Bearbeitung störungen usw.) sollten jedoch vollständig berücksichtigt werden, und die Festigkeit der Werkzeugspitze selbst sollte berücksichtigt werden.
zwei, Bogenförmiges Drehwerkzeug. Der bogenförmige Drehmeißel ist ein Drehmeißel, der sich durch eine bogenförmige Schneide mit einem kleinen Rundheits- oder Linienprofilfehler auszeichnet. Jeder Punkt der Bogenkante des Drehmeißels stellt die Spitze des bogenförmigen Drehmeißels dar. Dementsprechend liegt der Werkzeugpositionspunkt nicht auf dem Bogen, sondern in der Mitte des Bogens. Der bogenförmige Drehmeißel kann zum Drehen von Innen- und Außenflächen verwendet werden und eignet sich besonders zum Drehen verschiedener glatter (konkaver) Umformflächen. Bei der Wahl des Bogenradius des Drehmeißels sollte beachtet werden, dass der Bogenradius der Schneide des Zweipunkt-Drehmeißels kleiner oder gleich dem minimalen Krümmungsradius an der konkaven Kontur des Teils sein sollte. Um Bearbeitungsstörungen zu vermeiden, sollte der Radius nicht zu klein gewählt werden, da er sonst nicht nur schwierig zu fertigen ist, sondern auch der Drehmeißel durch schwache Werkzeugspitzenfestigkeit oder schlechte Wärmeableitung des Werkzeugkörpers beschädigt wird.
3. Wählen Sie Werkzeuge zum CNC-Fräsen
In der CNC-Bearbeitung werden häufig Flachboden fräser zum Fräsen der Innen- und Außenkonturen von Planteilen und Fräsebenen verwendet. Die empirischen Daten der relevanten Parameter des Tools sind wie folgt:
1. Der Radius RD des Fräsers sollte kleiner sein als der minimale Krümmungsradius Rmin der Innenkonturfläche des Teils, im Allgemeinen RD = (0,8-0,9) Rmin.
2. Die Bearbeitungshöhe des Teils H< (1/4-1/6) RD, um eine ausreichende Steifigkeit des Messers zu gewährleisten.
3. Beim Fräsen des Grundes der inneren Nut mit einem Flachboden fräser. Da die beiden Durchgänge am Nutgrund überlappt werden müssen und der effektive Radius der Unterkante des Werkzeugs Re=Rr ist, d. h. der Durchmesser ist d=2Re=2 (Rr), und der Werkzeugradius ist Re=0,95 (Rr) während der Programmierung. Für die Bearbeitung einiger dreidimensionaler Profile und Konturen mit variablen Fasenwinkeln werden häufig Kugelfräser, Ring fräser, Trommel fräser, Kegelfräser und Scheiben fräser verwendet.
Die meisten CNC-Werkzeugmaschinen verwenden serialisierte und standardisierte Werkzeuge. Für die Werkzeugaufnahmen und -köpfe von Wendeschneidplatten-Außendreh werkzeugen und Plandreh werkzeugen gibt es nationale Normen und Serienmodelle. Für Bearbeitungszentren und Werkzeugmaschinen mit automatischem Werkzeugwechsler wurden Werkzeughalter serialisiert und standardisiert: Beispielsweise lautet der Standardcode des Kegelschaft werkzeug systems TSG-JT und der Standardcode des Zylinderschaft werkzeug systems ist DSG-JZ. Außerdem ist für das ausgewählte Werkzeug eine genaue Messung der Werkzeuggröße erforderlich, um vor der Verwendung genaue Daten zu erhalten. Der Bediener gibt diese Daten in das Daten system ein und schließt den Bearbeitungsprozess durch Aufruf des Programms ab, wodurch qualifizierte Werkstücke bearbeitet werden.
CNC-Werkzeug spitze
Von wo aus beginnt das Werkzeug, sich an die angegebene Position zu bewegen?Daher muss zu Beginn der Programmausführung die Position bestimmt werden, an der sich das Werkzeug im Werkstück koordinatensystem zu bewegen beginnt. Diese Position ist der Startpunkt des Werkzeugs relativ zum Werkstück bei der Abarbeitung des Programms und wird daher als Programm startpunkt oder Startpunkt bezeichnet. Dieser Startpunkt wird im Allgemeinen durch die Werkzeugeinstellung bestimmt, daher wird dieser Punkt auch als Werkzeug einstellung punkt bezeichnet. Beim Übersetzen des Programms muss die Position des Werkzeug messpunktes richtig gewählt werden. Das Prinzip des Werkzeug einstell punktes ist: Erleichtern Sie die numerische Verarbeitung und vereinfachen Sie die Programmierung. Leicht auszurichten und während der Verarbeitung leicht zu überprüfen; Der verursachte Verarbeitungsfehler ist gering. Der Werkzeug einstell punkt kann am bearbeiteten Teil, aber auch an der Vorrichtung oder an der Werkzeugmaschine gesetzt werden. Um die Bearbeitung genauigkeit der Teile zu verbessern, sollte der Werkzeugeinstellpunkt möglichst auf den Konstruktions- oder Prozess nullpunkt des Teils gesetzt werden.
Im realen Betrieb der Werkzeugmaschine kann der Werkzeug positionspunkt des Werkzeugs durch manuellen Werkzeug einstell vorgang auf den Werkzeug messpunkt gelegt werden: Das heißt, die Übereinstimmung von "Werkzeug positionspunkt" und "Werkzeugeinstellpunkt". Der sogenannte "Werkzeug lagepunkt" bezieht sich auf den Positionierungs-Nullpunkt des Werkzeugs, und der Werkzeug lagepunkt des Drehmeißels ist die Werkzeugspitze bzw. der Mittelpunkt des Werkzeugspitzenbogens. Der Schaftfräser mit flachem Boden ist der Schnittpunkt der Werkzeugachse und der Unterseite des Werkzeugs, der Kugelfräser ist der Mittelpunkt der Kugel und der Bohrer ist die Spitze. Bei Verwendung des manuellen Werkzeug einstellbetriebs ist die Werkzeug einstell genauigkeit gering und die Effizienz gering. Einige Fabriken verwenden optische Werkzeug Einstellspiegel, Werkzeug Einstell Instrumente, automatische Werkzeugeinstellgeräte usw., um die Werkzeugeinstellzeit zu reduzieren und die Werkzeug einstell genauigkeit zu verbessern. Wenn das Werkzeug während der Bearbeitung gewechselt werden muss, sollte der Werkzeugwechselpunkt angegeben werden. Der sogenannte "Werkzeugwechselpunkt" bezeichnet die Position des Werkzeughalters, wenn dieser zum Werkzeugwechsel gedreht wird. Der Werkzeugwechselpunkt sollte sich außerhalb des Werkstücks oder der Vorrichtung befinden und das Werkstück und andere Teile dürfen beim Werkzeugwechsel nicht berührt werden.